Understanding Tube Fitting Types: A Comprehensive Guide
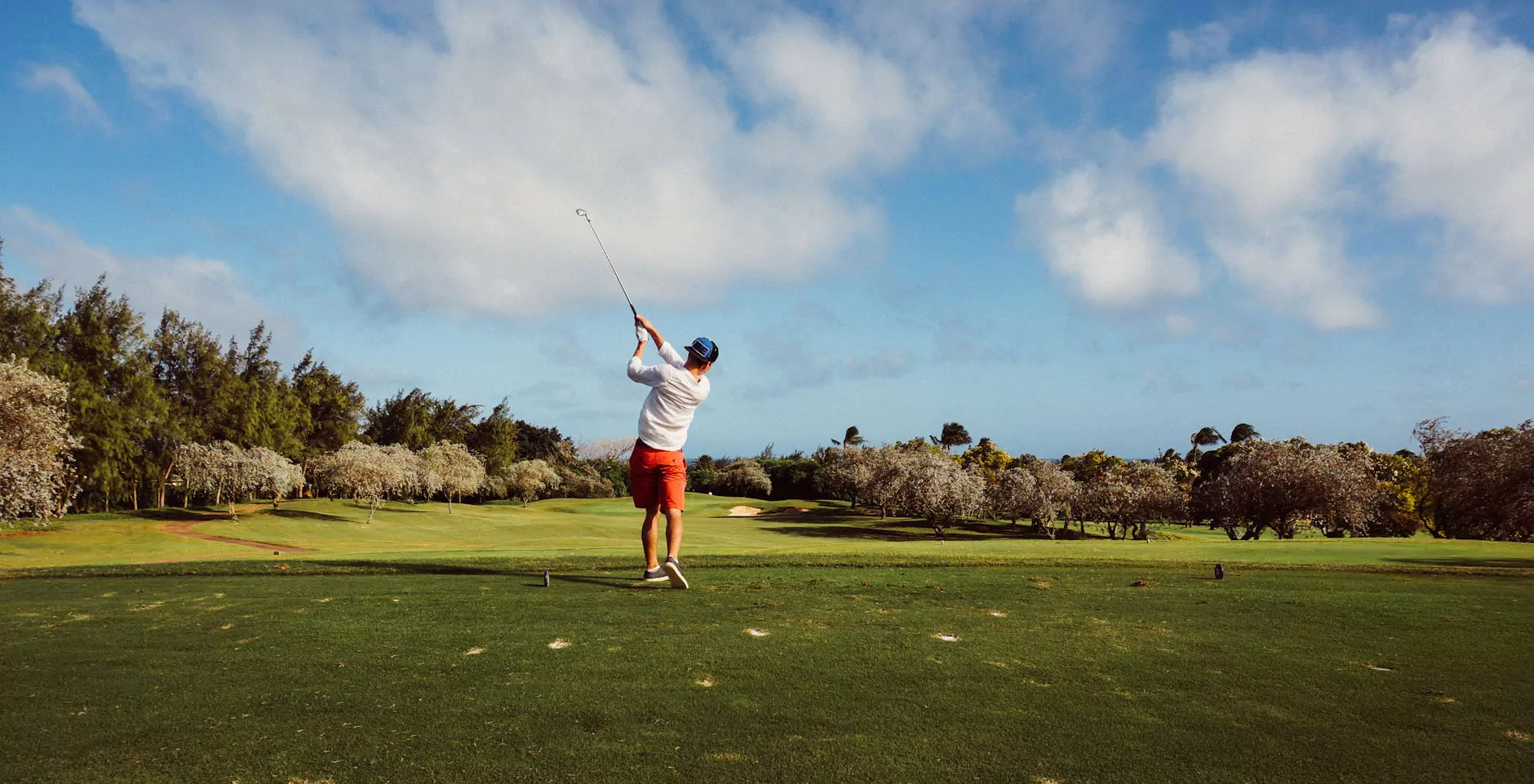
Tube fittings play a crucial role in various industrial applications. With a wide range of tube fitting types available, it is essential for businesses to understand which fittings best suit their specific requirements. This article provides an in-depth look at the different types of tube fittings, including their characteristics, applications, and selection criteria.
What are Tube Fittings?
Tube fittings are mechanical devices used to join two or more pieces of tube together. They ensure a secure connection that can withstand various operational conditions such as pressure, temperature, and environment. The right choice of tube fitting can significantly influence the efficiency and safety of a fluid handling system.
Types of Tube Fittings
Understanding the various tube fitting types is essential for making informed decisions. Below are the most common types of tube fittings and their unique characteristics:
1. Ferrule Fittings
Ferrule fittings are widely used in high-pressure applications. They use a ferrule (metal ring) that compresses against the tube when the fitting is tightened, creating a secure seal.
- Applications: Ideal for hydraulic and pneumatic systems.
- Advantages: Excellent sealing capability and durability.
2. Forged Pipe Fittings
Forged pipe fittings offer high strength and reliability. These fittings are made by shaping molten metal under pressure, which results in a dense and robust structure.
- Applications: Used in oil and gas, chemical industries, and water supply systems.
- Advantages: Superior resistance to shock and fatigue.
3. Threaded Pipe Fittings
Threaded pipe fittings are designed with external and internal threads for connection. They are simple to install and remove, making them convenient for maintenance.
- Applications: Suitable for low-pressure applications.
- Advantages: Easy installation and cost-effective.
4. Flanges
Flanges are flat pieces of metal used to connect pipes and allow for easy access for cleaning or inspections. They can be bolted together for a secure fit.
- Applications: Common in piping systems where ease of access is required.
- Advantages: Flexibility in assembly and ease of modification.
5. Check Valves
Check valves allow fluid to flow in one direction only, preventing backflow. They are essential for protecting equipment and ensuring process efficiency.
- Applications: Used in water pipes, chemical flow systems, and more.
- Advantages: Increased safety and reduced risk of contamination.
6. Ball Valves
Ball valves provide excellent control over fluid flow. They use a spherical disc to regulate flow and offer a tight seal when closed.
- Applications: Suitable for on/off control in high-pressure systems.
- Advantages: Quick operation and minimal pressure drop.
7. Needle Valves
Needle valves offer precise control over fluid flow through small orifices. They are commonly used in metering applications.
- Applications: Ideal for low-flow applications and instrumentation.
- Advantages: High accuracy in flow control.
8. Manifold Valves
Manifold valves centralize the control of multiple pipelines into a single component. This simplifies maintenance and reduces space requirements.
- Applications: Widely used in instrumentation and process control systems.
- Advantages: Streamlined operation and reduced risk of leaks.
9. Double Ferrule Tube Fittings
Double ferrule tube fittings provide reliable leak-proof connections through the use of two ferrules. They are commonly used in high-pressure applications.
- Applications: Used in chemical processing and instrumentation.
- Advantages: High resistance to vibration and thermal cycles.
10. Single Ferrule Tube Fittings
Single ferrule tube fittings incorporate one ferrule, making them suitable for low-pressure applications. They are easy to install and disassemble.
- Applications: Used in air, water, and gas lines.
- Advantages: Simple and efficient design.
11. NPT Fittings
NPT (National Pipe Tapered) fittings are widely used in the United States and feature tapered threads for sealing. This design ensures a tight fit.
- Applications: Common in plumbing and HVAC systems.
- Advantages: Easy to install and offers a leak-proof seal.
Choosing the Right Tube Fitting for Your Needs
Selecting the appropriate tube fitting type for your application involves considering several factors:
- Material Compatibility: Ensure the fitting material is compatible with the fluids being transported.
- Pressure and Temperature Ratings: Choose fittings that can handle the operating pressure and temperature conditions.
- Environment: Consider environmental factors such as corrosion, exposure to chemicals, and temperature fluctuations.
- Installation Space: Assess the available space for installation and maintenance, as some fittings require more room than others.
Benefits of Using Quality Tube Fittings
Investing in quality tube fittings offers a multitude of benefits for businesses:
- Increased Safety: Reliable fittings reduce the risk of leaks and accidents in high-pressure systems.
- Cost Efficiency: Quality fittings reduce the need for frequent replacements and maintenance, saving businesses money in the long run.
- Enhanced Performance: Well-designed fittings improve fluid flow and overall system efficiency.
Final Thoughts
In conclusion, understanding the various tube fitting types is integral to optimizing your systems and ensuring smooth operations. Selecting the right fittings can enhance safety, performance, and durability within your applications. For businesses looking to source top-quality fittings, consider partnering with reputable suppliers such as techtubes.in, which offers a wide range of options tailored to various industrial needs.
Knowing the strengths and applications of each fitting type allows you to make informed decisions that lead to greater efficiency and productivity. Embrace quality and precision in your connecting solutions to stand out in a competitive market.